Traditional Moulding
Injection moulding of plastic material is a manufacturing process where thermoplastic material is melted and injected, at high pressure, into a closed mould. After solidification, the mould is opened, and the final product is extracted.
Injection moulding is a delicate yet versatile process that enables the production of components and/or items of all shapes and sizes. Thanks to the large variety of machinery at our disposal, we are able to produce pieces of significant sizes.
This is why our injection moulding department is equipped with modern and innovative presses, with pressure capabilities that range from 30 to 700 tons. Customers come to us from a wide variety of sectors (e.g. automotive, electronic, interior design, health) and, thanks to our facilities, we are able to competently and professionally meet their requirements.
By building pilot moulds, which serve the purpose of moulding a pre-series of pieces, the customer can evaluate and physically test the finished product to ensure that it satisfies the production requirements. Furthermore, our measuring machine allows us to check the product’s tolerances even more thoroughly.
Polymer Choice
Innovative Moulding Techniques
Moulding department
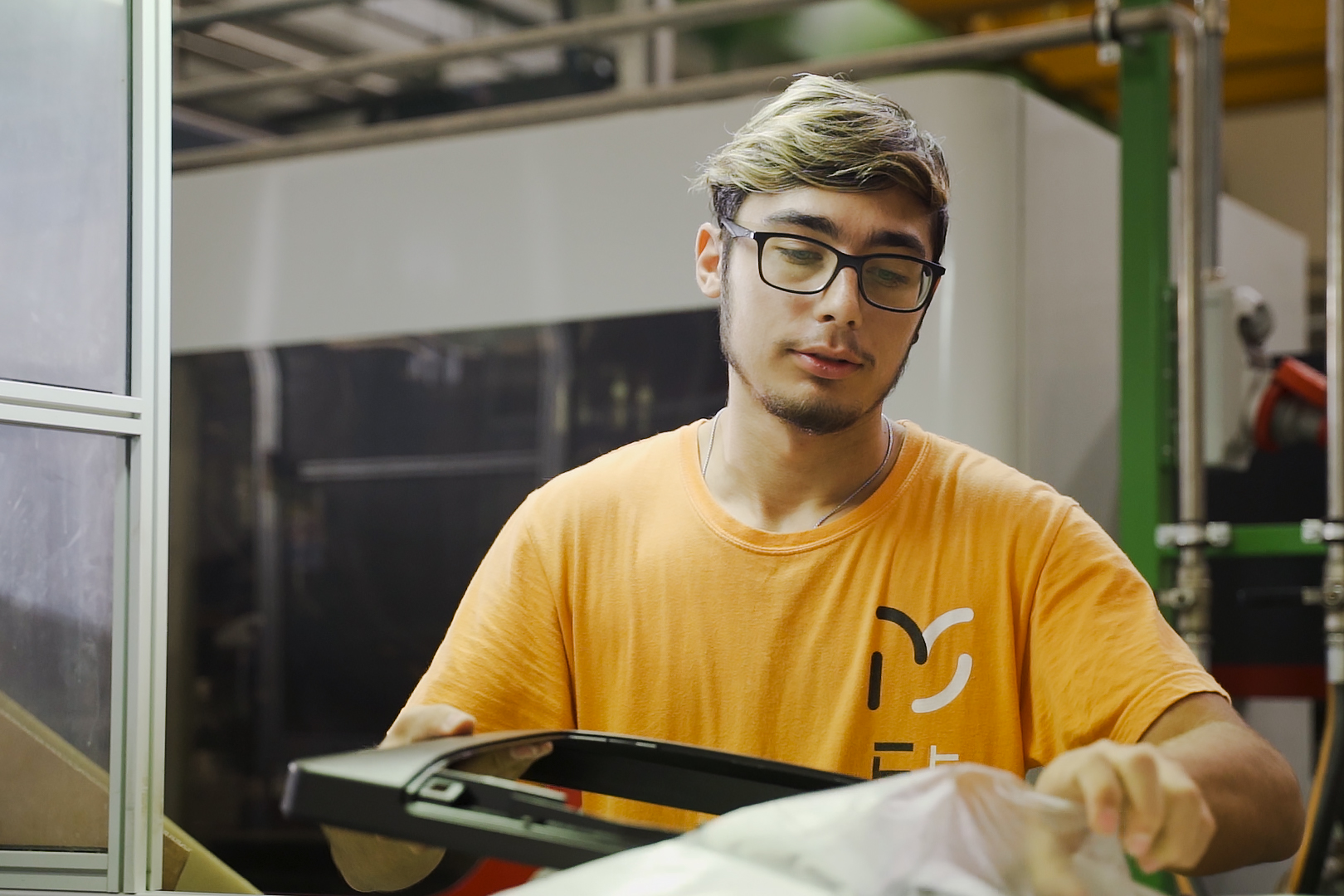
- Sandretto Injection Press 30 ton.
- Arburg Injection Press 50 ton.
- Negri Bossi Injection Press 70 ton
- Negri Bossi Injection Press 130 ton
- Negri Bossi Injection Press 180 ton. with cartesian robot
- Negri Bossi Injection Press 220 ton. with cartesian robot
- Arburg Injection Press 250 ton. with cartesian robot
- Negri Bossi Injection Press 330 ton. with cartesian robot
- Negri Bossi Injection Press 500 ton. with cartesian robot
- Negri Bossi Injection Press 700 ton. with cartesian robot
- Bauer Molding Gas System
- Molecular-sieving Dehumidifiers
- Thermoregulation System until 140°C
- CMM Wenzel Measuring Machine, measuring field of 1000x1600x800